Dans son usine d'Orange, Isover mise sur le recyclage de la laine de verre
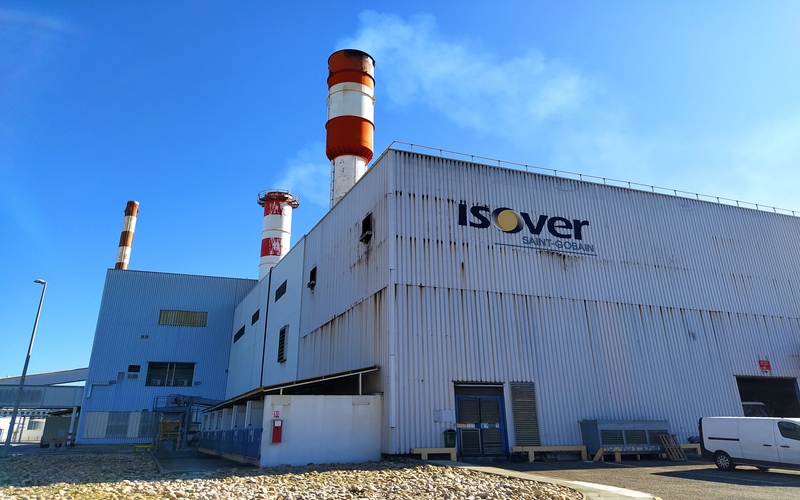
Dans son usine historique, construite en 1972 à Orange, dans le Vaucluse, Isover (enseigne du groupe Saint-Gobain) produit 125 000 tonnes de laine de verre par an. Il s'agit du plus gros site de production de laine de verre Isover à l'international. En France, l'usine est épaulée par celle de Chemillé (90 000 tonnes), et de Chalon-sur-Saône (23 000 tonnes).
Remplacer le sable par du calcin
À l'occasion d'une visite du site d'Orange, Rémi Jacques, son directeur, explique qu'historiquement l'usine s'approvisionnait en sable grâce à une carrière située à Bédoin, près du Mont Ventoux. Mais l'industriel ambitionne désormais de réduire – et même supprimer – le recours au sable dans ses produits d'ici 2030, ce qui est déjà le cas au sein de l'usine de Chalon-sur-Saône. Le remplacement du sable permet en effet de limiter les consommations d'énergie du four, avec un point de fusion à 1 450 °C pour le sable, contre 1 250 °C pour le calcin (verre recyclé).
Le four électrique en fonctionnement. Crédit photo : C.L.
Mais pour remplacer le sable, il est nécessaire d'augmenter la proportion de calcin (souvent issu du verre bouteille ou du verre plat de pare-brise), pour parvenir à un taux de 83 %.
Or, l'approvisionnement en calcin n'est pas toujours chose aisée, car il est de plus en plus recherché, et plus cher que le sable. Le directeur de l'usine souligne notamment que les Français restent mauvais élèves en matière de recyclage du verre, avec encore 46 % de bouteilles en verre non recyclées, contre un taux de recyclage à plus de 90 % en Allemagne.
Recycler les déchets de laine de verre en calcin
De fait, pour augmenter son taux de calcin, Isover mise sur son atelier Oxymelt, intégré à l'usine d'Orange depuis 1994. L'atelier récupère les déchets de laine de verre issus des rebuts de fabrication de l'usine, et plus récemment des chantiers de déconstruction, grâce à la démarche Isover Recycling.
Les rebuts de fabrication et déchets seront recyclés en calcin Oxymlet. Crédit photo : C.L.
Ces déchets sont ensuite transformés en calcin Oxymelt - qui se distingue par sa couleur marron, car il inclut tous les déchets annexes, que ce soit du papier, du carton ou du plastique.
À ce jour, l'usine d'Orange produit 18 tonnes d'Oxymelt par jour, mais la production pourrait monter à 24 tonnes. L'atelier doit d'ailleurs être modernisé, notamment avec un nouveau four SBM (Submerged Burner Melter) pour réduire les consommations d'énergie.
Le réemploi des déchets de laine de verre constitue une solution d'avenir, alors qu'ils représentent 75 000 de tonnes de déchets par an (souvent enfouis), et que ce nombre devrait monter à 120 000 tonnes d'ici 2030. Il devient donc urgent de recycler la laine de verre, d'autant plus que cette dernière est recyclable à l'infini.
Pour accélérer sur cet axe, Isover a mis en place sa démarche « Isover Recycling », enrôlant les acteurs du BTP (maîtres d'ouvrages, entreprises...) et des collecteurs agréés, qui font le tri et envoient les déchets de laine de verre comprimés par balle au centre de revalorisation Isover, qui se charge ensuite de les recycler.
Autre objectif environnemental du site : réduire de 50 % ses prélèvements en eau, alors que la région Provence Alpes Côte d'Azur (PACA) est en situation de stress hydrique d'avril à octobre. Le directeur de l'usine précise que 100 000 € seront investis cette année pour la réfection des canalisations enterrées afin de résorber les fuites, et pour recycler l'eau en boucle fermée, comme c'est déjà le cas dans l'usine de Chemillé.
Pour ses 40 ans, en 2012, l'usine d'Orange avait bénéficié d'un premier investissement de 20 millions d'euros pour la modernisation de son process industriel et la réduction de son impact sur l'environnement. Prochaine étape : une dizaine de millions d'euros devraient être investis d'ici 2030, notamment pour reconstruire le four de fusion électrique, dont la durée de vie est d'en moyenne 7 à 8 ans.
Claire Lemonnier
Photo de une : C.L.