À la découverte de l'unité de cartes électroniques d'Atlantic
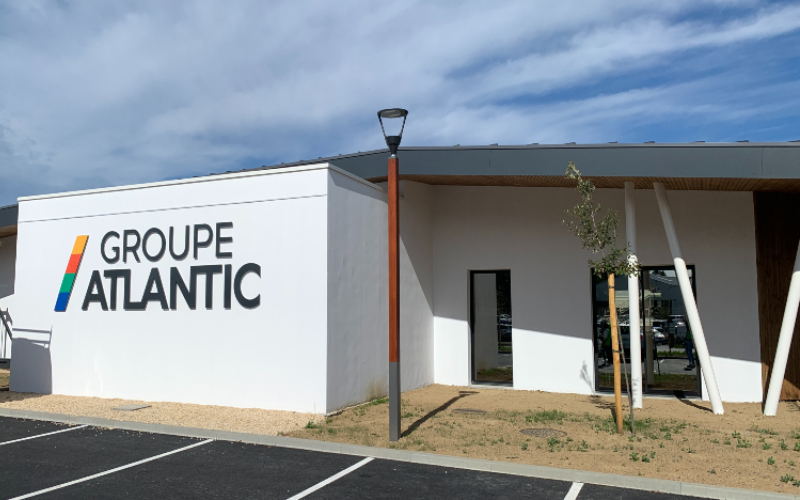
Après avoir annoncé investir 4,3 millions d’euros pour l’extension de son usine de production de cartes électroniques, dans le cadre de son « Plan électronique 2024 », le groupe Atlantic ouvrait son site historique de La Roche-sur-Yon à la presse en ce début du mois de juin. Outre les visites de son service d’assistance technique à la clientèle (SATC) et de son unité chauffe-eau, le groupe vendéen a ouvert les portes de son unité E2C, dédiée à la fabrication de cartes électroniques.
Le spécialiste du génie climatique prévoit entre autres une augmentation de 40 % des besoins en cartes électroniques pour l’ensemble de ses marques d’ici 2024, et souhaite donc porter leur production de 4 millions à 6 millions d’unités chaque année, grâce à un investissement important.
La zone Composants Montés en Surface (CMS)
Après s’être équipé d’une blouse et de languettes spéciales permettant de disperser l’électricité statique accumulée dans le corps, nous avons pu entrer dans la zone CMS (Composants Montés en Surface) de l’unité E2C. Comme son nom l’indique, cette zone est réservée à la pose des CMS sur le circuit imprimé des cartes électroniques.
Le personnel de l’unité E2C reçoit en effet les cartes électroniques « à nu », donc sans composants, mais avec un circuit imprimé en finition nickel-or, un alliage qui évite la corrosion et qui permet d’allonger la durée de vie de ces cartes. Ces dernières sont ensuite placées dans des machines qui utilisent la sérigraphie, afin de découper les emplacements réservés aux CMS et de les ajouter sur leur plage d’accueil respective.
Chaque composant est alors scanné par une caméra, qui a pour objectif de le reconnaitre et de le placer au bon endroit sur les différentes plages d’accueil. Ils sont par la suite soudés au circuit imprimé grâce à une technique de « brasage à la vague ». Avant de quitter la zone CMS, les points de soudure sont contrôlés et vérifiés au laser, et les cartes électroniques sont gravées d’un QR code unique, qui permet de les tracer. Ce sont au total pas moins de 100 000 composants qui sont déposés sur les circuits imprimés toutes les heures, pour une moyenne de 20 000 cartes électroniques fabriquées chaque jour, sachant qu’un appareil peut en contenir jusqu’à trois.
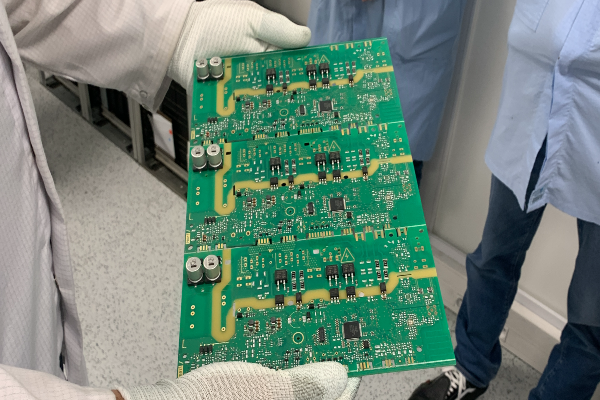
Un atelier où robots et opérateurs collaborent
Une fois sorties de la zone CMS, les cartes électroniques sont équipées de plus gros composants, dits composants « traversant ». Cette tâche est effectuée par des opérateurs, qui soudent les composants ajoutés, avant de contrôler visuellement chaque carte électronique. Cependant, certaines tâches pénibles peuvent dorénavant être réalisées par des robots collaboratifs, ce qui est par exemple le cas pour le déplacement des cartes vers un autre poste de travail.
Les cartes électroniques, souvent attachées trois par trois, sont découpées à l’unité et les opérateurs viennent ensuite y ajouter les plus gros composants en plastique. Enfin, les cartes partent vers les « carrousels », qui sont des espaces de travail composés de plusieurs postes, grâce à une plateforme pivotante. Ainsi, un opérateur installé à un carrousel peut travailler jusqu’à six postes de travail sans avoir à se déplacer, ce qui permet de limiter le coût, le nombre de postes, ainsi que la perte de temps lors des transferts de cartes vers d’autres espaces de travail.
C’est par ailleurs dans ces carrousels que sont réalisés les tests des cartes électroniques, leur vérification mais aussi le chargement de leurs programmes. Elles sont pour finir étiquetées avant d’être montées sur les différents boitiers.
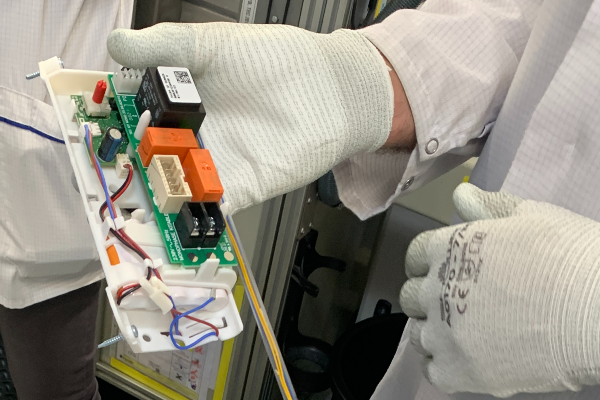
Robin Schmidt
Photo de une : ©RS