Isolation : bientôt des polyols biosourcés pour TPF Industrie ?
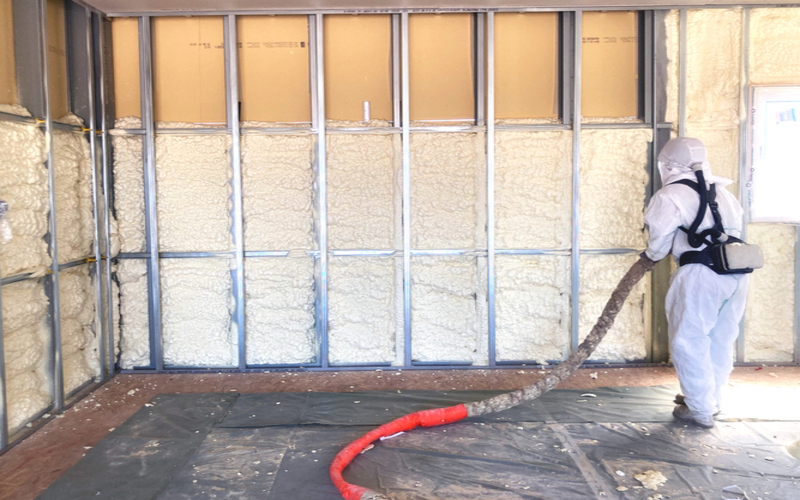
En 2019, le groupe Mirbat Groupe Holding (MGH) crée sa filiale Technique Polyuréthane France (TPF) Industrie, spécialisée dans la production de polyols destinés au marché du polyuréthane projeté pour l'isolation des bâtiments.
Le groupe investit alors 3,5 millions d'euros dans la création d'une usine à Noves, dans les Bouches-du-Rhône. Depuis mai 2020, l'usine produit environ 5 000 tonnes de polyols par an, avec une capacité de production jusqu'à 15 000 tonnes. Deux types de polyols y sont fabriqués pour différentes applications : à cellules ouvertes, notamment pour l'isolation des murs et sous-face de toiture, et à cellules fermées, en grande partie pour les sols.
« Actuellement, il y a deux sortes de polyuréthanes sur le marché de l'isolation du bâtiment. : il y a les panneaux sandwichs ou plaques, qui sont directement fabriqués en usine, et le polyuréthane projeté. Quand on assemble des plaques de polyuréthane, on a toujours un petit pont thermique a chaque assemblage de plaques. L'avantage du polyuréthane projeté, c'est qu'il n'y a pas de ponts thermiques, donc on a beaucoup moins de déperditions », explique Rodolphe Bagot, responsable de l'usine TPF Industrie.
Vers des polyols plus écologiques
Au niveau des étapes de fabrication des polyols, les matières sont reçues séparement, puis une dizaine de composants sont dosés avant d'être mélangés. Une étape de refroidissement est ensuite nécessaire pour atteindre une température d'environ 15 degrés avant d'ajouter un agent gonflant. Concernant ce dernier, Rodolphe Bagot souligne que TPF Industrie utilise une nouvelle génération d'hydro-fluoro-oléfines (HFO), qui n'émet pas de gaz à effet de serre, contrairement à l'hydro-fluoro-carbures (HFC), qui sera d'ailleurs interdit en Europe à partir de 2023.
A l'issue du processus de fabrication, en grande partie géré par un automate, le laboratoire réalise un contrôle en interne pour tester les polyols, vérifier leur dosage en eau, leur réactivité et leur densité, avant qu'ils ne soient conditionnés et envoyés aux clients. Enfin, pour fabriquer le polyuréthane, de l'isocyanate est mélangé au polyol.
Actuellement, l'équipe R&D réalise des tests pour produire de nouveaux polyols 100 % biosourcés, conçus à partir d'huiles végétales, de colza, de ricin, ou de noix de cajou.
« D'ici deux ou trois ans, on est en train de regarder pour créer une usine de production de polyols biosourcés. Cela veut dire qu'on achètera l'huile et on fera nous-même la transformation vers le polyol », précise Rodolphe Bagot.
En termes de recyclage, le responsable de l'usine ajoute que des copeaux de polyols ou de polyuréthane peuvent être réintégrés dans les machines et réutilisés.
Concernant les autres axes de développement de TPF Industrie, Rodolphe Bagot évoque également la possibilité d'élargir les applications hors du bâtiment.
Propos recueillis par Claire Lemonnier