Au cœur de la production de profilés PVC à Aizenay (85)
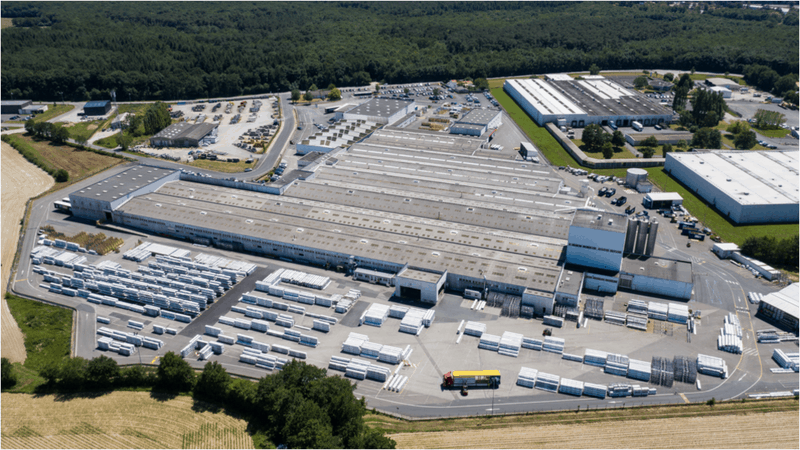
A Aizenay, en Vendée (85), l’usine Cougnaud fabrique 270 000 menuiseries Gimm et Les Menuiseries françaises par an. Sa spécificité ? Elle produit et transforme son propre PVC.
Autre particularité : elle dispose de son laboratoire de tests sur place et, depuis quelques mois, de son FabLab R&D. Les 33 750 m2 de l’usine abritent également 16 lignes d’extrusion de PVC, un atelier de plaxage, et un autre d’assemblage.
La production de PVC
La première étape consiste en la production de dry blend, c’est-à-dire du PVC extrudable sous forme de poudre. Ce dernier est constitué à 80% de résine de PVC, mélangé à des adjuvants : le modifiant choc qui augmente la résistance aux chocs, l’oxyde de titane qui blanchi, la craie qui améliore l’opacité, et le one pack qui détermine la couleur des profilés et stabilise la formule.
Les produits sont ainsi disponibles en 5 couleurs en teintés masse : blanc, sable, chêne doré, et deux nuances de gris RAL 7016 et RAL 7035. L’atelier de plaxage (collage d’un film coloré sur le PVC) propose quant à lui 16 coloris. Toute autre couleur qui n’en ferait pas partie peut également être appliquée grâce à une option laquage.
Autre point important : l'entreprise, investie dans une démarche de tri et de recyclage, recycle des chutes de PVC qui sont broyées. Les menuiseries fabriquées intègrent ainsi entre 30 et 40% de PVC recyclé.
Le processus d’extrusion
Au niveau des lignes d’extrusion, la matière première arrive de l’extrudeuse à 195°C puis est injectée sous pression dans un moule appelé « filière ». Le processus d’extrusion se termine par un refroidissement dans une eau à 10°C, qui permet le durcissement du profilé.
Les menuiseries sont ensuite assemblées par des opérateurs, qui disposent d’un écran pour les guider dans les étapes à réaliser. Des robots d’assemblage « d’une centaine de milliersd’euros » seront également mis en service à partir du mois de septembre, annonce Ludovic Lecart, directeur de l’usine.
L’usine ne propose pas uniquement des menuiseries rectangulaires, mais aussi des menuiseries cintrées et des baies coulissantes. Chaque commande, sur-mesure, est livrée en 3 semaines (10 jours pour les commandes les plus urgentes).
Le laboratoire de tests
Dès la phase de production du PVC, les matières premières sont contrôlées par le CSTB. Il en va de même pour le produit fini, avec un audit réalisé tous les 6 mois par l’organisme. La certification NF nécessite également de réaliser de nombreux tests. Ainsi, le laboratoire qualité prélève des échantillons et vérifie la colorimétrie et la géométrie, mais aussi l’endurance, et la résistance à l’eau, à l’air et au vent des menuiseries.
Roadshow : déjà plus 20 000 km parcourus par le camion de formation
En projet depuis 3 ans, un roadshow a été lancé en début d’année. Un camion sillonne la France - avec à son bord Philippe Barbeau, responsable technique, qui présente les nouveautés des marques Gimm et Menuiseries françaises et dispense des formations sur-mesure aux poseurs. « Notre but est d’aller au-devant des besoins des clients », explique-t-il.
Parmi les formations proposées : la prise de côte et la pose des produits Gimm et Menuiseries françaises dans le respect du DTU 36.5, ou encore une formation aux réglages.
« Paradoxalement les poseurs ne connaissent pas toujours bien les réglages. Au début ils me disent "ça fait 30 ans que je fais comme cela", puis quand ils sortent de la formation ils se rendent compte qu’ils ont appris plein de choses », constate le responsable technique.
Chaque module de formation dure entre 1h et 1h30. À son issue, le formateur propose un quizz ludique sur la télévision installée dans le camion.
Le camion, qui a déjà parcouru 20 000 km et s’est arrêté dans 30 villes, se rendra même en Corse en octobre prochain. Plus de 400 personnes ont déjà été formées à travers la France, et le planning est rempli jusqu’à mi-novembre 2019.
Le camion de formation. ©C.L.
L'intérieur du camion aménagé. ©C.L.
C.L.
Photo de une : ©R. Arnaud / Hyperlink